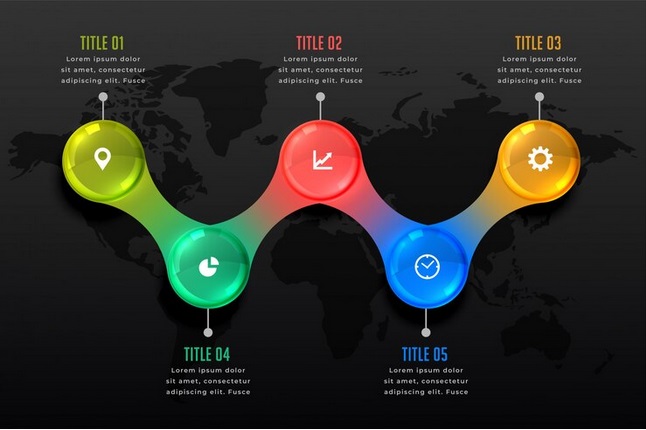
En muchas oportunidades nos han planteado el utilizar un software del tipo MRP (Material Requirements Planning – Planificación de Requerimientos de Materiales) para el cálculo de los tiempos de elaboración en procesos industriales y en particular pharma.
Argumentan los partidarios de esta idea que en última instancia el tiempo (de máquina o de mano de obra directa) puede considerarse un insumo más como lo son las materias primas activas, los exciepientes y el material de empaque.
De hecho son varios los paquetes de software que simplemente permiten incluir los tiempos de elaboración como parte de la fórmula de producto, eventualmente con una simple ‘marca’ indicando que se trata de tiempo y no de material.
Si lo que buscamos es exclusivamente determinar el costo directo de un producto el criterio me parece aceptable, siempre que los tiempos reales de elaboración sean razonablemente próximos a los estándares. Determinar los estándares de mano de obra en operaciones no automatizadas suele ser menuda tarea, incluso para un especialista, de modo que los ‘desvíos’ pueden ser sumamente significativos.
Pero aún dejando de lado el problema de determinar con exactitud el insumo ‘tiempo’ (de máquina o mano de obra directa) requerido para determinada fórmula, resulta que hay varios motivos que hacen que un cálculo MRP sea claramente insuficiente para una programación de los tiempos de elaboración:
- El recurso ‘tiempo’ se consume aunque no lo esté utilizando. A diferencia de cualquier insumo material, la máquina parada o el operario inactivo igual consumen su tiempo … aún cuando el mismo no se incorpore al producto.
- Las operaciones de manufactura deben necesariamente desarrollarse en un cierto orden, y muchas veces (no siempre) una operación no puede iniciarse hasta tanto se haya concluido lo anterior. En una producción pharma de comprimidos una secuencia habitual podría ser a) fraccionamiento; b) mezcla; c) compresión, d) laqueado o revestimiento; e) blisteado; f) estuchado. La b) no puede iniciarse antes de concluida la a) y la c) debe esperar a que finalice la b); en las restantes podría suceder (bajo ciertas condiciones que exceden el alcance de esta nota) un cierto ‘solapamiento’.
- Complementariamente al punto anterior, cuando un equipo (u operario) está ejecutando determinada operación, se encuentra ‘indisponible’ para cualquier otra operación. Hablamos de ‘capacidad finita’ a diferencia de los insumos materiales los cuales en general (hay excepciones) pueden programarse a ‘capacidad infinita’.
Por los puntos detallados más algunos complementos es que TIXTOOLS le da un tratamiento específico al tema de los tiempos y plazos de elaboración, mediante un sub-sistema (add-on) de ‘Secuenciación de Carga de Máquinas’.
La meta y resultado principal de este proceso es determinar el orden de las sucesivas operaciones de manufactura correspondientes a las múltiples ordenes de producción en proceso. Este orden propuesto conocido como ‘programación’ se basa a las siguientes reglas:
- Para cada O/P las operaciones se ejecutan en forma consecutiva, siguiendo el orden y duración establecidos en la secuencia de operaciones del producto.
- Salvo que se defina solapamiento de operaciones sucesivas, ninguna operación puede iniciar antes de concluída la operación anterior.
- No puede haber más de una operación programada simultaneamente sobre el mismo equipo (o asignada al mismo operario)
- Las operaciones ya iniciadas tienen prioridad sobre las simplemente proyectadas.
En base a las reglas anteriores el sistema de Secuenciación de Carga TIXTOOLS asigna períodos de tiempo (fecha-hora de inicio y fecha-hora de finalización) a cada uno de los recursos productivos; sean equipos o mano de obra directa, mediante un proceso de cálculo en batch.
El orden de procesamiento de cada una de las O/P’s puede establecerse y modificarse manualmente en forma directa o indirectamente asignando niveles de prioridad a cada O/P.
El resultado principal es una planilla de secuenciación de carga de máquinas en formato de gráfica de Gantt. Cada barra representa una operación programada y las líneas rojas vinculan las sucesivas operaciones de la misma orden.
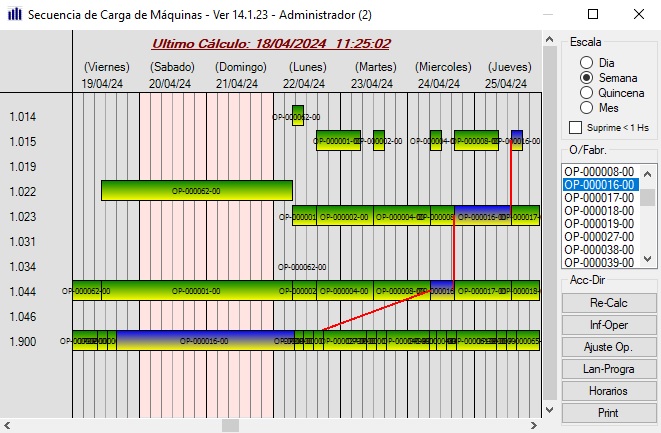
Los mismos resultados se presentan también en formatos de tablas de secuencia de carga por O/P y también por equipo y operario.
Dos sub-productos importantes del proceso son los siguientes:
- La determinación del ETA (fecha y hora estimada de terminación) de cada O/P y junto con el eventual retraso / adelantamiento respecto de lo solicitado.
- Siendo que aparecen ‘vacíos’ en los cuales no aparecen operaciones programadas, el sistema determina la ‘densidad de carga’. Corriendo el proceso de secuenciación con distintos ordenamientos o prioridades, podemos optimizar la densidad de carga correspondiente a cada simulación. En resumen, una herramienta que en minutos permite optimizar la utilización de los recursos productivos y reducir los plazos de entrega, asumiendo una tarea que desarrollada manualmente insume mucho tiempo y produce inevitables errores.
Si tienes demoras en tus entregas o un ‘cuello de botella’ en tu capacidad instalada ¿ por qué no tenemos una charla acerca de lo que puede hacer TIXTOOLS por la optimización del aprovechamiento de tu capacidad ? Y por tu bolsillo, porque adquirir máquinas, tercerizar operaciones o tomar personal cuesta muchísimo más que implementar un sistema decente. E incluso interfasearlo con tu ERP que seguramente cumple su función administrativo contable a la perfección.
Llamame (+54 9 11 3430 4617) o escribeme (ebauer@tixtools.com.ar) para más información.
Ing. Ernesto Pablo Bauer Egerer
TIXTOOLS Soluciones – Director